Les dessous du Grand Paris Express (2ème partie)
« Nous sommes dans des zones à forte densité de population, près de la capitale du pays, avec la dimension politique que peut revêtir ce genre de projet, qui va mettre plus de 10 ans à être complétement opérationnel. L’entrepreneur est donc face à une multitude d’aléas », prévient Guillaume Sauvé, président d’Eiffage Génie Civil. Le décor est planté. Car qui dit chantiers hors-normes, dit aléas et solutions hors-normes. Après les premiers appels d’offres lancés en 2014, les grandes entreprises françaises de génie civil ont pris possession du sous-sol francilien. Au total, 68 nouvelles gares vont sortir de terre, mais surtout 200km de tunnels seront creusés au total. Une prouesse nécessitant des moyens d’exception. À commencer par de gigantesques tunneliers.
Les tunneliers, machines des temps moderne
« Un tunnelier, c'est une très grosse usine souterraine qui va réaliser les futurs tunnels du Grand Paris Express, explique Alain Truphémus (1), directeur adjoint de la Ligne 16 au sein de la Société du Grand Paris (SGP). Ils fonctionnent 24h/24, avec environ une vingtaine de compagnons pour le faire fonctionner. C’est une machine tout-en-un : elle creuse le tunnel, elle excave le terrain et ensuite, elle pose le futur revêtement du tunnel constitué de voussoirs en béton, qui vont constituer des anneaux. Cette usine souterraine permet également d’évacuer les déblais qui sont excavés. C’est une machine gigantesque qui fait 10m de diamètre, 110m de long et qui pèse plus de 1500 tonnes. Nous allons en avoir 9 sur la Ligne 16 pour réaliser les 30km du tunnel entre Noisy-Champs et Saint-Denis-Pleyel. » À leur inauguration, chacune de ces machines a été baptisée d’un prénom féminin (Amandine, Aïcha, Laurence…).
Sur la Ligne 16 par exemple, Armelle a eu 3km de tunnel à creuser, entre Aulnay et le Blanc-Mesnil, un autre tunnelier venant à sa rencontre pour faire la jonction. Au jour le jour, la bonne marche de ces usines souterraines tient à deux paramètres : à la tête du tunnelier qui creuse et, à l’autre extrémité, à l’évacuation des déblais. Et là, un défi de taille attendait ingénieurs et opérateurs.
La valorisation des déchets, un enjeu majeur
Dès le début des chantiers, la Société du Grand Paris a insisté auprès des entreprises de construction sur la valorisation de 45 millions de tonnes de déblais que l’ensemble des chantiers produiront en 15 ans de travaux. « La valorisation des déblais est un processus plus compliqué qu’il n’y paraît, car on ne peut pas réutiliser les terrains excavés n’importe où et n’importe comment, souligne Benoît Maureau, directeur chez Eiffage Génie Civil. Où sont les trous de carrière qui méritent d’être remplis
par des terrains compatibles ? Que peut-on directement recycler parmi les matériaux que l’on extrait ? Tous les acteurs déploient beaucoup d’énergie pour trouver des solutions à tous ces défis. » Chez Eiffage, dès l’attribution du lot 1 de la Ligne 16, les ingénieurs ont compris l’importance du dossier : pour pouvoir faire avancer les tunneliers rapidement, il fallait identifier la nature de 4500 tonnes excavées quotidiennement, pour les expédier le plus rapidement possible là où elles seraient réutilisées, sans immobiliser de sites de stockage le temps d’une analyse traditionnelle, entre 5 et 7 jours.
En partenariat avec le Commissariat à l’énergie atomique (CEA), Eiffage a travaillé deux ans à la mise au point et au brevet d’un nouvel outil, baptisé Carasol, capable d’identifier les déblais en moins de 2 heures. « Pour déterminer la composition chimique des déblais permettant de les orienter vers le bon exutoire, il faut faire des prélèvements pour des tests, explique Pascal Hamet, directeur du projet du lot 1 de la Ligne 16 chez Eiffage Infrastructure. Jusqu’à présent, obtenir les résultats de ces tests nécessitait une semaine d’attente. Ce délai aurait été beaucoup trop long par rapport aux superficies d’emprises dont nous disposons sur ce type de chantier. Carasol permet des gains de temps, et une réduction à la fois de notre empreinte carbone et des frais de fonctionnement des chantiers. Le dispositif Carasol était donc vital. » À l’image de la valorisation des déblais, problèmes et imprévus ont été multiples sur les chantiers.
Aléas et solutions : le pain quotidien des ingénieurs
À Saint-Denis-Pleyel par exemple, des défis taille XXL attendaient Eiffage dès le début du chantier en 2018, trois tunnels devant s’y croiser sous le réseau ferré. En surface, des bâtiments ont dû être achetés pour être rasés ; en sous-sol, il a fallu dépolluer la terre, imbibée d’hydrocarbures à cause de la présence d’une station-service dans le passé. « À Saint-Denis-Pleyel se croisent les lignes 14, 15 et 16, poursuit Pascal Hamet. La taille de ce chantier a été le premier défi remarquable à relever, par sa superficie et sa profondeur (près de 35m). Préalablement au terrassement, il a fallu réaliser ce que nous appelons des fondations spéciales, des parois moulées notamment. Mais lorsque cette opération a démarré, les chantiers équivalents de la Ligne 15-sud (entre Pont de Sèvre et Noisy-Champs) avaient déjà démarré et nous étions confrontés à une surchauffe d’activité pour ces métiers de fondation. La difficulté majeure était donc de trouver des entreprises et des ateliers de réalisation de parois moulées en quantité suffisante pour pouvoir assurer la construction des 24 ouvrages (5 gares et 19 ouvrages annexes). » Sur le lot 1 de la Ligne 16, la course contre la montre a toujours été permanente, et ce dès l’attribution de l’appel d’offres.
Le principal défi réside dans la simultanéité des chantiers, et dans la disponibilité des outils de production. Par ailleurs, des structures aux dimensions inhabituelles, aux portées inhabituelles nécessitent des modes de calcul eux-mêmes inhabituels. « C’est quelque chose que le bureau d’études d’Eiffage maîtrise aujourd’hui parfaitement alors que la définition des ouvrages n’était pas tout à fait aboutie, souligne Pascal Hamet. Pour la bonne et simple raison que ce chantier fait partie de ceux que la SGP a lancé dans des délais record. Généralement, pour concevoir un tel projet et lancer des appels d’offres, il faut entre 7 et 10 ans. » Dans le cas du GPE, les chantiers ont été lancés au bout de 5 ans seulement, avec un degré d’aboutissement et de calculs de structures réalisés à l’origine par les cabinets d’études agréés par la SGP, nécessairement à affiner.
Les difficultés techniques et les impératifs des cahiers des charges n’ont généralement laissé que peu de marge de manœuvre aux entreprises de génie civil : impossibilité d’avoir des virages serrés comme dans le métro, avec des rames filant à 110km/h, obligation de creuser les tunnels entre 20 et 40m de profondeur (jusqu’à 52m à Saint-Maur-Créteil) en rencontrant parfois une géologie récalcitrante, comme dans certains tronçons de la Ligne 15-Sud. « Au total, ce seront environ 130000 voussoirs qui seront posés, explique Guillaume Pons (2), directeur de projet à la SGP. La vitesse moyenne de progression d’un tunnelier est de 12m par jour mais elle dépend de la géologie. Le tunnelier avance le mieux dans un horizon constant. Une fois les réglages terminés, les techniciens sont bien rodés et la moyenne de progression augmente. Mais notons qu’un tunnelier, on sait quand il part mais, au regard des aléas techniques, son arrivée n’est pas arithmétique ! »
À chantier démesuré, risques multipliés. « Sur les chantiers comme celui du GPE, il existe deux familles de risques, souligne Benoît Maureau. La première, c’est l’impact sur les bâtis avoisinants. Quand vous creusez le sous-sol avec un tunnelier de 110m de long, vous pouvez passer sous des bâtiments sensibles. Quand vous construisez une gare, vous pouvez faire souffrir un bâtiment environnant. Il faut donc avoir des méthodes de construction adaptables à ce qui a été prévu dans les études. La seconde famille de risques est de rencontrer, au moment où vous creusez, quelque chose de différent de ce qui était prévu. Lorsque l’on traverse telle ou telle couche de terrain, il faut pouvoir anticiper des contraintes spécifiques à la nature du sous-sol. C’est ce qui rend indispensable les reconnaissances géotechniques préalables les plus poussées, mais aussi la mise en place de mesures d’auscultation et d’instrumentation pour assurer la surveillance des bâtiments en temps réel. »
À cela s’ajoute la complexité de faire fonctionner tout un écosystème d’intervenants, entre donneur d’ordre, équipes d’ingénierie, sociétés partenaires et collectivités territoriales. « Il arrive parfois que pour diverses raisons les emprises de travaux ne soient pas disponibles en temps et en heure, remarque Benoît Maureau. À nous alors de réagir pour adapter nos méthodes de construction en concertation avec la SGP, et compenser la perte de temps initiale. »
Tout pour éviter de gêner les riverains
L’intégralité des chantiers du GPE se déroule donc dans des zones urbanisées. Avec 68 nouvelles gares, les collectivités concernées subissent forcément des désagréments. Là aussi, les intervenants du BTP ont fait tout leur possible pour atténuer l’impact des nuisances. Pour cela, Imed Ben Fredj, directeur des supports opérationnels chez Eiffage Génie Civil, a mis en place sur chacun des chantiers de nouvelles méthodes constructives : « La plupart du temps, pour pouvoir construire des ouvrages enterrés, et notamment les gares, nous utilisons une technique – pour des raisons des délais et de nuisance aux riverains – consistant à “fermer la boîte” afin de travailler à l’intérieur. C’est ce que nous appelons “travailler en taupe”. » Objectif : estomper le bruit des machines, le bruit des allers-venues des camions ou encore les émissions de poussière.
« En ce qui concerne le bruit des chantiers, nous disposons de plusieurs solutions, précise Benoît Maureau. Nous capotons le plus possible tous les moteurs thermiques ; si nous pouvons passer sur des moteurs électriques, c’est évidemment mieux. Surtout, en matière d’organisation, nous faisons tout notre possible pour que le flux de circulation sur nos chantiers permettent aux véhicules de se déplacer essentiellement, voire uniquement en marche avant. Et quand la marche arrière, associée à l’avertisseur sonore de sécurité, est inévitable, nous avons remplacé les klaxons de recul par ce que nous appelons le “cri du lynx”, qui est une alerte plus atténuée… Croyez-moi, tous ces détails comptent et font la différence pour les riverains. »
Pour préserver l’environnement immédiat des chantiers, les entreprises ont également dû faire preuve d’ingéniosité, à commencer par le nettoyage des roues des camions pour éviter de souiller la voie publique. « Toujours concernant les camions, ajoute Benoît Maureau, nous nous imposons la rigueur la plus stricte possible dans la gestion du trafic, pour les camions arrivant sur les chantiers comme pour ceux qui en repartent. Nous essayons autant que possible de prévoir ce trafic en amont, afin de prévenir tous les acteurs locaux de nos contraintes, et réduire ainsi la gêne occasionnée, surtout lors des grandes phases de travaux. Il y a eu une vraie prise de conscience des acteurs du BTP sur ce point depuis plusieurs années, et nous avons fait de nets progrès dans ce domaine. »
Ces progrès affichés sont à mettre sur le compte d’une politique de RSE volontariste de la part des grands groupes. La prochaine grande étape sera de transformer totalement la flotte des camions pour réduire l’empreinte carbone du BTP, comme le détaille Pascal Hamet : « Sur la Ligne 16, nous avons proposé, dans le cadre de notre démarche “bas carbone”, d’investir dans une flotte de camions qui roulent au gaz. Ce n’est pas si anecdotique que cela peut paraître : ce qui était nouveau dans ce projet était notre exigence à utiliser des chemins, sur les lieux définitifs de dépôt des matériaux de chantier, qui ne sont pas carrossables pour les camions roulant habituellement au gaz. Notre but ici est de réduire notre empreinte carbone, pour éviter d’avoir recours aux camions diesel habituels. Ces camions au gaz préfigurent la propulsion électrique. » Volvo et Scania ne sont en effet pas encore tout à fait prêts à livrer des engins de chantiers 100% électriques.
Toutes ces solutions – des tunneliers au système Carasol en passant par la bonne gestion du trafic des camions – n’ont finalement qu’un seul but : tenir les délais fixés par la Société du Grand Paris. Avec comme premier objectif, une mise en service partielle pour l’ouverture des Jeux olympiques de Paris en 2024. Mais ça, c’est une autre histoire.
« Nous sommes dans des zones à forte densité de population, près de la capitale du pays, avec la dimension politique que peut revêtir ce genre de projet, qui va mettre plus de 10 ans à être complétement opérationnel. L’entrepreneur est donc face à une multitude d’aléas », prévient Guillaume Sauvé, président d’Eiffage Génie Civil. Le décor est planté. Car qui dit chantiers hors-normes, dit aléas et solutions hors-normes. Après les premiers appels d’offres lancés en 2014, les grandes entreprises françaises de génie civil ont pris possession du sous-sol francilien. Au total, 68 nouvelles gares vont sortir de terre, mais surtout 200km de tunnels seront creusés au total. Une prouesse nécessitant des moyens d’exception. À commencer par de gigantesques tunneliers.
Les tunneliers, machines des temps moderne
« Un tunnelier, c'est une très grosse usine souterraine qui va réaliser les futurs tunnels du Grand Paris Express, explique Alain Truphémus (1), directeur adjoint de la Ligne 16 au sein de la Société du Grand Paris (SGP). Ils fonctionnent 24h/24, avec environ une vingtaine de compagnons pour le faire fonctionner. C’est une machine tout-en-un : elle creuse le tunnel, elle excave le terrain et ensuite, elle pose le futur revêtement du tunnel constitué de voussoirs en béton, qui vont constituer des anneaux. Cette usine souterraine permet également d’évacuer les déblais qui sont excavés. C’est une machine gigantesque qui fait 10m de diamètre, 110m de long et qui pèse plus de 1500 tonnes. Nous allons en avoir 9 sur la Ligne 16 pour réaliser les 30km du tunnel entre Noisy-Champs et Saint-Denis-Pleyel. » À leur inauguration, chacune de ces machines a été baptisée d’un prénom féminin (Amandine, Aïcha, Laurence…).
Sur la Ligne 16 par exemple, Armelle a eu 3km de tunnel à creuser, entre Aulnay et le Blanc-Mesnil, un autre tunnelier venant à sa rencontre pour faire la jonction. Au jour le jour, la bonne marche de ces usines souterraines tient à deux paramètres : à la tête du tunnelier qui creuse et, à l’autre extrémité, à l’évacuation des déblais. Et là, un défi de taille attendait ingénieurs et opérateurs.
La valorisation des déchets, un enjeu majeur
Dès le début des chantiers, la Société du Grand Paris a insisté auprès des entreprises de construction sur la valorisation de 45 millions de tonnes de déblais que l’ensemble des chantiers produiront en 15 ans de travaux. « La valorisation des déblais est un processus plus compliqué qu’il n’y paraît, car on ne peut pas réutiliser les terrains excavés n’importe où et n’importe comment, souligne Benoît Maureau, directeur chez Eiffage Génie Civil. Où sont les trous de carrière qui méritent d’être remplis
par des terrains compatibles ? Que peut-on directement recycler parmi les matériaux que l’on extrait ? Tous les acteurs déploient beaucoup d’énergie pour trouver des solutions à tous ces défis. » Chez Eiffage, dès l’attribution du lot 1 de la Ligne 16, les ingénieurs ont compris l’importance du dossier : pour pouvoir faire avancer les tunneliers rapidement, il fallait identifier la nature de 4500 tonnes excavées quotidiennement, pour les expédier le plus rapidement possible là où elles seraient réutilisées, sans immobiliser de sites de stockage le temps d’une analyse traditionnelle, entre 5 et 7 jours.
En partenariat avec le Commissariat à l’énergie atomique (CEA), Eiffage a travaillé deux ans à la mise au point et au brevet d’un nouvel outil, baptisé Carasol, capable d’identifier les déblais en moins de 2 heures. « Pour déterminer la composition chimique des déblais permettant de les orienter vers le bon exutoire, il faut faire des prélèvements pour des tests, explique Pascal Hamet, directeur du projet du lot 1 de la Ligne 16 chez Eiffage Infrastructure. Jusqu’à présent, obtenir les résultats de ces tests nécessitait une semaine d’attente. Ce délai aurait été beaucoup trop long par rapport aux superficies d’emprises dont nous disposons sur ce type de chantier. Carasol permet des gains de temps, et une réduction à la fois de notre empreinte carbone et des frais de fonctionnement des chantiers. Le dispositif Carasol était donc vital. » À l’image de la valorisation des déblais, problèmes et imprévus ont été multiples sur les chantiers.
Aléas et solutions : le pain quotidien des ingénieurs
À Saint-Denis-Pleyel par exemple, des défis taille XXL attendaient Eiffage dès le début du chantier en 2018, trois tunnels devant s’y croiser sous le réseau ferré. En surface, des bâtiments ont dû être achetés pour être rasés ; en sous-sol, il a fallu dépolluer la terre, imbibée d’hydrocarbures à cause de la présence d’une station-service dans le passé. « À Saint-Denis-Pleyel se croisent les lignes 14, 15 et 16, poursuit Pascal Hamet. La taille de ce chantier a été le premier défi remarquable à relever, par sa superficie et sa profondeur (près de 35m). Préalablement au terrassement, il a fallu réaliser ce que nous appelons des fondations spéciales, des parois moulées notamment. Mais lorsque cette opération a démarré, les chantiers équivalents de la Ligne 15-sud (entre Pont de Sèvre et Noisy-Champs) avaient déjà démarré et nous étions confrontés à une surchauffe d’activité pour ces métiers de fondation. La difficulté majeure était donc de trouver des entreprises et des ateliers de réalisation de parois moulées en quantité suffisante pour pouvoir assurer la construction des 24 ouvrages (5 gares et 19 ouvrages annexes). » Sur le lot 1 de la Ligne 16, la course contre la montre a toujours été permanente, et ce dès l’attribution de l’appel d’offres.
Le principal défi réside dans la simultanéité des chantiers, et dans la disponibilité des outils de production. Par ailleurs, des structures aux dimensions inhabituelles, aux portées inhabituelles nécessitent des modes de calcul eux-mêmes inhabituels. « C’est quelque chose que le bureau d’études d’Eiffage maîtrise aujourd’hui parfaitement alors que la définition des ouvrages n’était pas tout à fait aboutie, souligne Pascal Hamet. Pour la bonne et simple raison que ce chantier fait partie de ceux que la SGP a lancé dans des délais record. Généralement, pour concevoir un tel projet et lancer des appels d’offres, il faut entre 7 et 10 ans. » Dans le cas du GPE, les chantiers ont été lancés au bout de 5 ans seulement, avec un degré d’aboutissement et de calculs de structures réalisés à l’origine par les cabinets d’études agréés par la SGP, nécessairement à affiner.
Les difficultés techniques et les impératifs des cahiers des charges n’ont généralement laissé que peu de marge de manœuvre aux entreprises de génie civil : impossibilité d’avoir des virages serrés comme dans le métro, avec des rames filant à 110km/h, obligation de creuser les tunnels entre 20 et 40m de profondeur (jusqu’à 52m à Saint-Maur-Créteil) en rencontrant parfois une géologie récalcitrante, comme dans certains tronçons de la Ligne 15-Sud. « Au total, ce seront environ 130000 voussoirs qui seront posés, explique Guillaume Pons (2), directeur de projet à la SGP. La vitesse moyenne de progression d’un tunnelier est de 12m par jour mais elle dépend de la géologie. Le tunnelier avance le mieux dans un horizon constant. Une fois les réglages terminés, les techniciens sont bien rodés et la moyenne de progression augmente. Mais notons qu’un tunnelier, on sait quand il part mais, au regard des aléas techniques, son arrivée n’est pas arithmétique ! »
À chantier démesuré, risques multipliés. « Sur les chantiers comme celui du GPE, il existe deux familles de risques, souligne Benoît Maureau. La première, c’est l’impact sur les bâtis avoisinants. Quand vous creusez le sous-sol avec un tunnelier de 110m de long, vous pouvez passer sous des bâtiments sensibles. Quand vous construisez une gare, vous pouvez faire souffrir un bâtiment environnant. Il faut donc avoir des méthodes de construction adaptables à ce qui a été prévu dans les études. La seconde famille de risques est de rencontrer, au moment où vous creusez, quelque chose de différent de ce qui était prévu. Lorsque l’on traverse telle ou telle couche de terrain, il faut pouvoir anticiper des contraintes spécifiques à la nature du sous-sol. C’est ce qui rend indispensable les reconnaissances géotechniques préalables les plus poussées, mais aussi la mise en place de mesures d’auscultation et d’instrumentation pour assurer la surveillance des bâtiments en temps réel. »
À cela s’ajoute la complexité de faire fonctionner tout un écosystème d’intervenants, entre donneur d’ordre, équipes d’ingénierie, sociétés partenaires et collectivités territoriales. « Il arrive parfois que pour diverses raisons les emprises de travaux ne soient pas disponibles en temps et en heure, remarque Benoît Maureau. À nous alors de réagir pour adapter nos méthodes de construction en concertation avec la SGP, et compenser la perte de temps initiale. »
Tout pour éviter de gêner les riverains
L’intégralité des chantiers du GPE se déroule donc dans des zones urbanisées. Avec 68 nouvelles gares, les collectivités concernées subissent forcément des désagréments. Là aussi, les intervenants du BTP ont fait tout leur possible pour atténuer l’impact des nuisances. Pour cela, Imed Ben Fredj, directeur des supports opérationnels chez Eiffage Génie Civil, a mis en place sur chacun des chantiers de nouvelles méthodes constructives : « La plupart du temps, pour pouvoir construire des ouvrages enterrés, et notamment les gares, nous utilisons une technique – pour des raisons de
« En ce qui concerne le bruit des chantiers, nous disposons de plusieurs solutions, précise Benoît Maureau. Nous capotons le plus possible tous les moteurs thermiques ; si nous pouvons passer sur des moteurs électriques, c’est évidemment mieux. Surtout, en matière d’organisation, nous faisons tout notre possible pour que le flux de circulation sur nos chantiers permettent aux véhicules de se déplacer essentiellement, voire uniquement en marche avant. Et quand la marche arrière, associée à l’avertisseur sonore de sécurité, est inévitable, nous avons remplacé les klaxons de recul par ce que nous appelons le “cri du lynx”, qui est une alerte plus atténuée… Croyez-moi, tous ces détails comptent et font la différence pour les riverains. »
Pour préserver l’environnement immédiat des chantiers, les entreprises ont également dû faire preuve d’ingéniosité, à commencer par le nettoyage des roues des camions pour éviter de souiller la voie publique. « Toujours concernant les camions, ajoute Benoît Maureau, nous nous imposons la rigueur la plus stricte possible dans la gestion du trafic, pour les camions arrivant sur les chantiers comme pour ceux qui en repartent. Nous essayons autant que possible de prévoir ce trafic en amont, afin de prévenir tous les acteurs locaux de nos contraintes, et réduire ainsi la gêne occasionnée, surtout lors des grandes phases de travaux. Il y a eu une vraie prise de conscience des acteurs du BTP sur ce point depuis plusieurs années, et nous avons fait de nets progrès dans ce domaine. »
Ces progrès affichés sont à mettre sur le compte d’une politique de RSE volontariste de la part des grands groupes. La prochaine grande étape sera de transformer totalement la flotte des camions pour réduire l’empreinte carbone du BTP, comme le détaille Pascal Hamet : « Sur la Ligne 16, nous avons proposé, dans le cadre de notre démarche “bas carbone”, d’investir dans une flotte de camions qui roulent au gaz. Ce n’est pas si anecdotique que cela peut paraître : ce qui était nouveau dans ce projet était notre exigence à utiliser des chemins, sur les lieux définitifs de dépôt des matériaux de chantier, qui ne sont pas carrossables pour les camions roulant habituellement au gaz. Notre but ici est de réduire notre empreinte carbone, pour éviter d’avoir recours aux camions diesel habituels. Ces camions au gaz préfigurent la propulsion électrique. » Volvo et Scania ne sont en effet pas encore tout à fait prêts à livrer des engins de chantiers 100% électriques.
Toutes ces solutions – des tunneliers au système Carasol en passant par la bonne gestion du trafic des camions – n’ont finalement qu’un seul but : tenir les délais fixés par la Société du Grand Paris. Avec comme premier objectif, une mise en service partielle pour l’ouverture des Jeux olympiques de Paris en 2024. Mais ça, c’est une autre histoire.
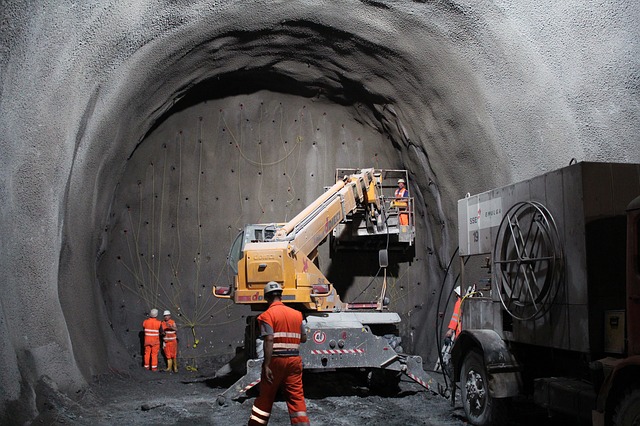